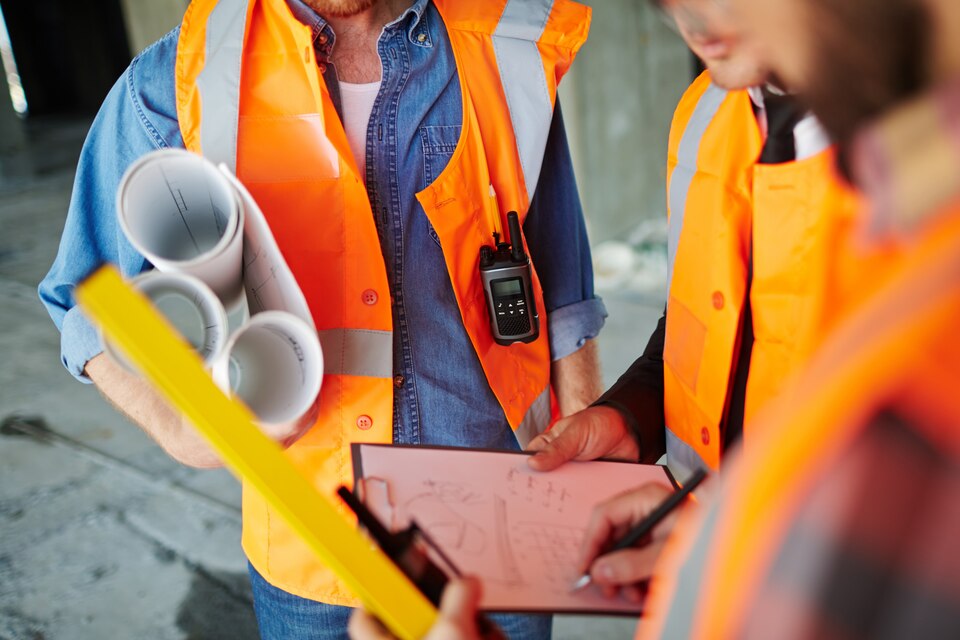
Enhancing Safety, Efficiency, and Productivity
Introduction
The industrial operations are complex environments where a minor hiccup means generating losses for productivity, safety, and money. These industrial monitoring systems use real-time data regarding equipment performance, process, and environmental conditions to advise a decision if any interventions are required. The trend toward increased automation and connectivity in industries makes advanced and effective integrated monitoring systems an indispensable means of operational excellence, compliance, and protection of personnel in the future.
Industrial monitoring systems include a large variety of applications: safety assurance, process optimization, and condition-based maintenance. In addition to the traditional wide-ranging functions through the utilization of modern technologies like IoT sensors and cloud computing, by applying AI-driven analytics, these systems will also predict issues that may arise in operations before they actually happen; thus leading within the safety of generated profit.
What are System Monitoring Tools?
Monitored by system monitoring, these tools are basically parameters that are really structured for continuous observation of industrial processes and equipment. From simple sensors to complex software platforms capable of aggregating data, analyzing performance and offering effective insights, this kind of tool can serve as an example of different ranges. The sole objective of having these tools is to accomplish operation within a parameter that is safe and most efficient.
Typically, system monitoring tool measurements focus on:
Tuning and pressure:
Critical to the integrity of machinery and preventing over-boiling or high-pressure points.
Vibrations and sound levels:
Detects mechanical problems (like misalignments or bearing failures) before they become serious.
Energy consumption:
Allows industries to optimize power usage and cut costs on operations.
Environmental conditions:
Environments are continually monitored with respect to indicators – such as air quality, humidity, and levels of chemicals – to ensure health and safety compliance with respect to environmental regulations.
Higher-end tricks will also have predictive analytics so that the operators can foresee possible failures and act proactively to rectify it. Avoiding the reactive side of situations is one of the foundations of contemporary industry management.
Industrial Safety Monitoring Systems
Indeed, industrial operations are notorious for being the most unsafe given the numerous hazardous conditions that they can present, and the serious harm they can cause to both employees and assets. A monitoring system for industrial safety is designed to investigate each unsafe condition and immediately notify its operator so that it can be addressed at the earliest possible time.
There are several components of industrial safety monitoring systems:
•Gas and Chemical Detection Systems:
These are indispensable in industries that handle critical hazardous materials. They mainly leak and monitor unsafe concentrations of such materials.
•Fire and Explosion Detection Systems:
Combines sensors and alarms that would immediately alert people at risk to any apparent risk from fire or explosion·
•Machine Guarding Systems:
Monitors the work proximity of workers against dangerous machinery specifying automatic shutdowns to avoid accidents.
•Emergency Response Systems:
Integrated communication and alert mechanisms for speedy evacuation or containment processes during emergencies.
Preventech’s modular solution on safety monitoring describes how advanced technologies can offer higher benefits to industrial safety. It is not only possible to connect it with existing equipment but even merge it with real-time data for a higher level of assurance in coverage, even when older industrial setups are put into place.
Industrial Condition Monitoring Systems
Condition monitoring systems, which are imperative for the health of industrial equipment, involve continuous observation or tracking of key parameters that offer insights into equipment health to prevent any unforeseen breakdown. The main benefit of using a condition monitoring system is that it allows the prediction of maintenance.
Some of the types of condition monitoring are:
• Vibration analysis:
It detects imbalances, misalignments, wearing of bearings in shafts and splits in rotating machinery.
• Thermography:
Identifies some parts that are overheating, meaning either electrical or mechanical malfunction.
• Oil Analysis:
Determine the purity of the lubricants contaminating them or wearing out machines.
• Ultrasound monitoring:
This is a medium through which problems in the compressed air systems, steam traps, and other mechanical components are recognized.
Condition monitoring systems would practically give industries life extension to equipment, reduce the cost of maintenance, and reliability will increase.
Perspectives on Process Monitoring of Industrial Systems
Process monitoring is the overall functionality in which industries manage their entire operations activities to be consistent with, meet the quality, and produce as much efficiency as possible. Rather effective process monitoring integrates continuous data collection and analysis to identify changes and improve performance.
At the managerial side, there are a number of ways process monitoring is critical.
- Increased Control in Quality: The product is expected to be of required quality standards through immediate adjustments that come with real-time data.
- Increase in Productivity: It helps operational efficiency by identifying bottlenecks and wastes which should be avoided in process monitoring.
- Compliance with Regulations: Continuous monitoring over time also ensures compliance with all the industry health and safety regulations thus avoiding any future fines or shutdowns in the organization.
- Reduction in costs because early detection on time saves wastage, saves rework, and saves downtime and thus reduces operational costs.
Preventech’s integrated monitoring solutions demonstrate that process monitoring and condition monitoring can be put together within one solution to give all-around visibility. Such systems provide real-time feedback and advanced analytics that help industries to maximize performance while also being safe.
Conclusion
Thus, it has become very vital and important in itself as one of the most useful tools employed today by industrial activities in the modern world-the real-time monitoring system which also keeps track and ensures safety, enhances efficiency, and reliability for the respective operations. Safety monitoring, condition tracking, and process optimization-all of these systems make proactive management possible for enhanced decision-making.
Advances such as the modular monitoring system by Preventech represent a bright future for industrial supervision. Integrating the newest sensors, real-time analytics, and fast integration into existing infrastructure, such a system is said to offer incredible protection and productivity for industries which intend to keep themselves competitive in this increasingly complicated context. For an industry to benefit from more or less such a situation, investing in some proper monitoring system is therefore not just advisable-however, it has been termed an essential move.
Emerged as such, a soundly implemented industrial monitoring strategy usually ensures the sustained success, brings about a safer environment at work, and enhances operational productivity-it is, therefore, a most basic aspect of any industrial undertaking.