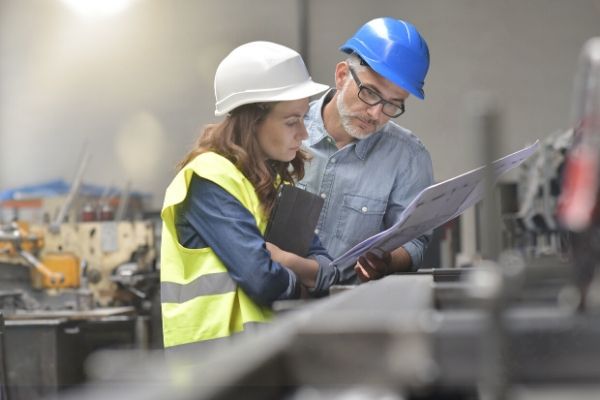
Industrial Preventive Control Systems
Introduction
There are industrial domains where the priority groups are the safety of operations and the efficiency of operations. The damage that incurs due to industrial equipment, due to various reasons such as mechanical failures, human errors, and surrounding hazardous environmental conditions may become very high. One of the very important roles that a preventive industrial control system does include rehabilitation of risk created through improper handling of safety and efficiency of operations through detection of real-time hazards and actions before they lead to possible accidents that endanger the lives of workers, equipment, and infrastructure.
Definition of Preventive Control
Proactive measures that keep the industrial operations safe from potential risk is termed as preventive control. Unlike the other reactive measures, which would take action after an event of an incident, preventive control identifies risks in the initial stages and adopts mechanisms to avert incidents. The controls may include real-time monitoring tools that continuously monitor the operational status of the machines, safety interlocks, and automatic shutdown systems. Preventive control would, therefore, minimize downtime, save costs on maintenance, and enhance safety in workplaces.
Industrial Preventive Maintenance
Preventive maintenance in industries is the traditional inspection and servicing of equipment that guards against unexpected failure and ensures optimal performance. Such a measure would form part of the strategy aimed at keeping the industrial system reliable and safe in operation. The preventive activities covered by these maintenance practices are periodic checks, timely replacement of worn-out parts as well as calibration of safety devices. Effective maintenance programs help industries to prevent or minimize costly breakdowns and pro-long machinery lifespan. Preventive maintenance can be time-interval or equipment use-based. More advanced such as the Preventech solution can go further by enabling condition-based sensor data use ensuring that maintenance would occur when needed and not prematurely-so-to-reduce operational disruption and resource wastage.
Define Industrial Control Systems
An industrial control system (ICS) is an integrated set of hardware and software that can be used for setting and controlling any industrial process. Hence, it is very critical in industries such as manufacturing, energy, and utilities, where precision and safety become very significant. ICS control mechanisms include supervisory control and data acquisition (SCADA) systems, distributed control systems (DCS), etc., and programmable logic controllers (PLCs).
ICS shall be working on the principle of ensuring a smooth, efficient, and safe operation of processes, which constantly monitors the process variables and makes corrections to the operational routines, mostly in terms of the actual control functional organization of different devices, and prevents any important deviation from process accidents or production inefficiencies.
Industrial Control System Examples
Examples of industrial control systems abound across many industries. Here is a sample of some of the most common:
•SCADA System:
SCADA systems are also quite popular in utilities and the energy sector. They centralize operations and allow real-time monitoring of large processes involving systems like power grids and water distribution channels.
•DCSs (Distributed Control systems):
Most chemical and pharmaceutical industries use DCS to control complex operational processes by distributing their control functions across multiple controllers.
•PLCs (programmable logic controllers):
These are used widely in manufacturing and assembly lines, controlling a specific process, such as robotic arms and conveyor belts.
•Building Management Systems (BMS):
Commercial Buildings and factories typically utilize rents by using these control systems. They often control HVAC, lighting, and security services with energy efficiency.
Preventech’s Modular Control System-an advanced example of industrial control system created for the betterment of safety through the integration of existing equipment, real-time hazard detection services, and automatic shutdown when necessary.
Conclusion
Industrial control systems for preventive measures have alleviated modern industries from becoming more organized, effective, secure, and reliable. But with applying proactive measures or technologies, companies can significantly lower their potential risks and operational costs thanks to Preventech’s innovative solutions. Adoption of strong industrial controls and preventive maintenance ensures that potential issues are detected early enough to eliminate costly disruptions. At the end of the day, a well-designed preventive control system will promote better workplace safety, more productivity, and eventually result in a longer competitive advantage in the industrial arena.