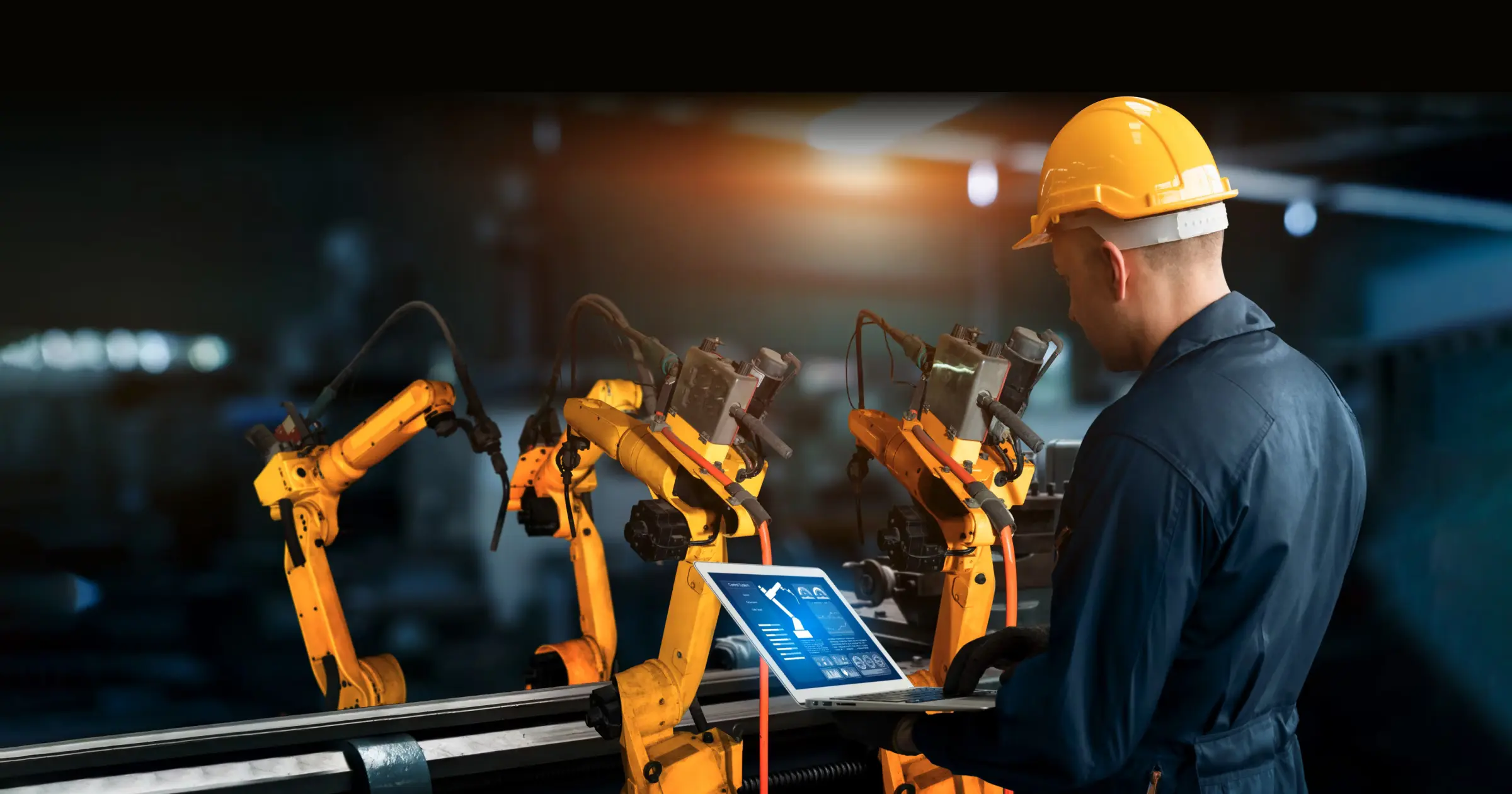
Industrial Monitoring Systems
Introduction
String, twisted in an enormous knot of technicality into which anything short of the highest of human knowledge may lead and noise crawling through the microphone-line between you and me in response: a tiny glitch in an automated environment can make a world of difference-one that you can almost see by the naked eye when it happens-to productivity, safety or even actual haulage. From industrial monitoring systems comes mitigation and more efficient approaches to an industrial facility’s operation through real-time visibility into equipment performance, process conditions, and environmental factors-as a catalyst for proactive decision-making. With an increasingly high degree of automation coupled with extensive interconnectivity within industries, more advanced monitoring solutions play a key role in sustaining operational excellence, ensuring compliance, and protecting employees.
This really broad category of applications for an industrial monitoring system is safety assurance, process optimization, and condition-based maintenance. For instance, they are based on recent concepts such as IoT sensors, cloud computing, and AI-based analytics to predict a problem before it happens to create a safer and more profitable workplace environment.
What are System Monitoring Tools?
Tools and equipment for monitoring process systems are space specific devices designed to provide continuous monitoring of industrial processes and equipment. Systems monitoring encompasses the entire range from simple sensors to high-end sophisticated software platforms that collect and analyze performance data and derive actionable intelligence from that data. The primary objects of such tools are to ensure the system operates within safe and efficient parameters, as much as under conditions that can be dealt with proactively instead of reactively using a head-end system.
Typical system monitoring parameters include the following:
- Temperature and Pressure: Critical to the safety margins from overheating or dangerously high-pressure levels.
- Vibration and Sound Level: Useful in identifying soon-to-be serious mechanical issues like misalignment or bearing failures.
- Energy Consumption: Help industries minimize energy usage and reduce operating costs.
- Ambient Conditions: Monitoring factors like exposure to unsafe levels of air quality, humidity, and chemicals ensures compliance with health, safety, and environmental regulations.
Advanced tools include predictive analytics whereby an operator can use the information to preempt possible failures. Such preventive measures as opposed to curative ones are characteristic of modern industry.
Industrial Safety Monitoring Systems
Safety is one of the important goals for operations in industries where presence hazardous conditions which could cause injury to employees or damage to equipment. Industrial safety monitoring systems are designed to detect unsafe conditions and notify operators about it immediately, so corrections can be implemented at once.
The systems have a number of components, including the following:
- Gas and Chemical Detection Systems: Essential for industries dealing with hazardous substances, the systems are meant to detect leaky or unsafe concentrations of the particular substance.
- Fire and Explosion Detection Systems: This system detects the risk of fire and explosions using several alarms and sensors.
- Machine Guarding Systems: These monitor the distance of workers from dangerous machinery and can automatically shut down equipment to prevent accidents.
- Emergency Response Systems: They provide integrated pathways of communication and warning when the emergency triggers evacuation or containment procedures.
One example of how modern technology can enhance safety in the industrial sector is a modular safety monitoring solution by Preventech. Such technologies can be integrated with existing equipment allowing real-time data flow which guarantees above average protection even in legacy facilities.
Safety is one of the important goals for operations in industries where hazardous conditions could injure employees or even cause equipment damage. Industrial safety monitoring systems are designed to detect unsafe conditions and notify operators about it immediately so that corrections can be implemented at once. Modular safety monitoring solutions, such as Preventech’s, are some of the advanced technologies that can improve safety in industrial operations. Integrating with existing equipment so that real-time data is being used, this solution makes it possible to have a higher level of protection, even at older industrial facilities.
Industrial Condition Monitoring Systems
Condition monitoring systems are designed to keep industrial equipment in a healthy state. These systems witness the main parameters continuously and bring forth highly.
Predictive maintenance is the main benefit of condition monitoring-heal immediate ailments before one ends up draining costly maintenance costs. Condition Monitoring is vibration analysis: it detects imbalances, misalignments, and bearing wear, Thermography: identification of overheating components, which could indicate an electrical or mechanical fault, use of infrared cameras. Oil analysis monitoring the quality of lubricants to aid in detecting contamination or wear in machinery, and ultrasound monitoring to classify problems in compressed air systems, steam traps, and mechanical components.
So, condition monitoring systems would ensure lasting equipment lifetime and less maintenance costs with an overall increase in reliability.
Perspectives on Process Monitoring of Industrial Systems
Process Monitoring means a complete survey of the workflows in industrial operations so that consistency, quality, and efficiency are maintained. It comprises continuous collection and analysis of data to discover deviations and optimize performance.
A management perspective can give different potential advantages in the way process monitoring.
- Better Quality Control because real-time data allows modifications as soon as a product does not meet the quality requirement.
- More Productivity: Process monitoring identifies all bottlenecks and operational inefficiencies, then identifies these to streamline procedures.
- Compliance with Regulations: Continuous monitoring ensures compliance with regulations and standards for safety-time, thus reducing associated fines or closure.
- Savings: Anomalies can be detected early, thereby leading to savings on both wasted resources and reworking and reducing downtime.
Preventech monitoring solutions have been truly integrated, representing an example of what could be accomplished by process and condition monitoring. Such systems will then benefit industries regarding safety, optimal during real-time feedback and advanced analytics.
Conclusion
With time, industrial monitoring systems have transformed into indispensable tools in industrial operations-they give the real-time information and intelligence that are essential for maintaining safety, efficiency, and reliability. They facilitate safety monitoring, condition tracking, or process optimization-all important proactive management and improved decision-making.
One of the next-generation solutions on the market is Preventech’s modular monitoring system. Integrating cutting-edge sensors, real-time analytics, and seamless incorporation with existing infrastructure, these systems offer unmatched protection and efficiency. The industries need a strong monitoring system that is not just recommended but mandatory for strong performance as the environment becomes increasingly sophisticated and demanding.
The well-implemented industrial monitoring strategy will ensure long-term gain, contribute better safety at the workplace, and boost the operational performance of any industrial enterprise; hence, it is an all-important component of every industrial enterprise.